When most people think about sustainability at a company like Cisco, they envision solar arrays and smart cities – and we certainly have those! But humming quietly on the roof of every building is a significant energy consumer, the air conditioning. So just as we innovate solutions for the Internet of Everything, we also search for ways to improve facility energy efficiency in many ways that aren’t obvious to building occupants.

Heating, Ventilation, and Air-Conditioning (HVAC) technologies are a significant part in the facility energy consumption story, particularly as we look to cool our data centers and technology labs. An issue with HVAC systems is that units become less efficient over time, as heat transfer areas become fouled and corroded. Cleaning periodically improves conductivity and efficiency, but corrosion has a cumulative effect.
Historically, the problem has been that you could not coat the heat transfer elements (coils and fins) without sacrificing heat transfer efficiency. Typical coatings are purely for protecting coils from corrosion. The coating basically becomes an insulator, like wrapping the transfer elements in a blanket, and reduces the efficiency of the HVAC system.
Recently, we found an innovative process developed by HVAC Armor to apply an aluminum coating that binds and restores deteriorating HVAC coils and metal surfaces. This process rejuvenates corroded coils and recovers lost efficiencies. The application provides 1-2 mm thick coating that penetrates up to 6 layers of the coil to insure maximum airflow through the coils. It’s a multistage process that includes not only the coating to the exterior coils and interior refrigerant line but also a general inspecting and repair of the system along with replacing filters
At our facilities in San Jose, California, HVAC Armor cleaned, coated, and treated a collection of large outdoor packaged units, and we tested them after each process.
- Total post-cleaning energy savings from the HVAC Armor treatments ranged from 23% to 32% per unit
- Savings were verified by measuring the pre and post coefficient of performance (COP) of the units
- Inspection process uncovered a number of other issues with the units including plugged filters and refrigerant leaks
- Updated cleaning procedures eliminate the need for cleaning chemicals and control of the associated run-off
- Cleaning is required less frequently and can be done more simply with low-pressure water
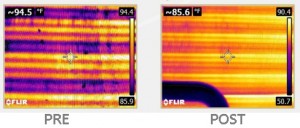
We are now applying HVAC Armor to Cisco’s HVAC systems nationwide. With similar results in a first deployment phase of 50 projects, we expect savings of over 16 million kilowatt hours per year, 6,700 tons of carbon emissions which represents almost 16 million miles driven by a typical passenger vehicle.
Of course, it will all happen in the background where our employees, customers, and partners are unlikely to notice — unless, with The Drifters, they happen to be “Up On the Roof.”
CONNECT WITH CISCO
LET US HELP
Call us: 1.800.553.6387 - Ext 118
US/Can | 5am-5pm Pacific Other Countries